Turning Around
In conversation with woodworker Ken Freeman of Vermont Rolling Pins
When Ken Freeman started his woodturning career in 2007, he focused on architectural restoration, replicating ornate balusters and porch posts to replace damaged originals in older homes. He soon expanded his business, Vermont Custom Woodturning, to include creating turned wood furniture parts, as well. But when the financial crisis hit and the construction industry was at a standstill, he needed another way to earn money.
Vermont Rolling Pins was Ken’s lifeline in the recession economy. His artisan rolling pins, which he makes in a variety of designs using maple, cherry, and walnut hardwood, were quickly noticed by the New York Times and Women’s Day and thus became wildly popular. They’ve been in steady demand ever since, with a spike during the pandemic baking boom.
Now, Ken juggles both ventures, rehabbing historic houses and crafting rolling pins simultaneously. He spends hours each day working on his lathe, while his wife Cyndi runs the companies. “We joke that she's a CEO, CFO, and everything else, and I'm the laborer out in the shop,” he says. Here, he shares how he fell into woodturning and why his rolling pins are so special.
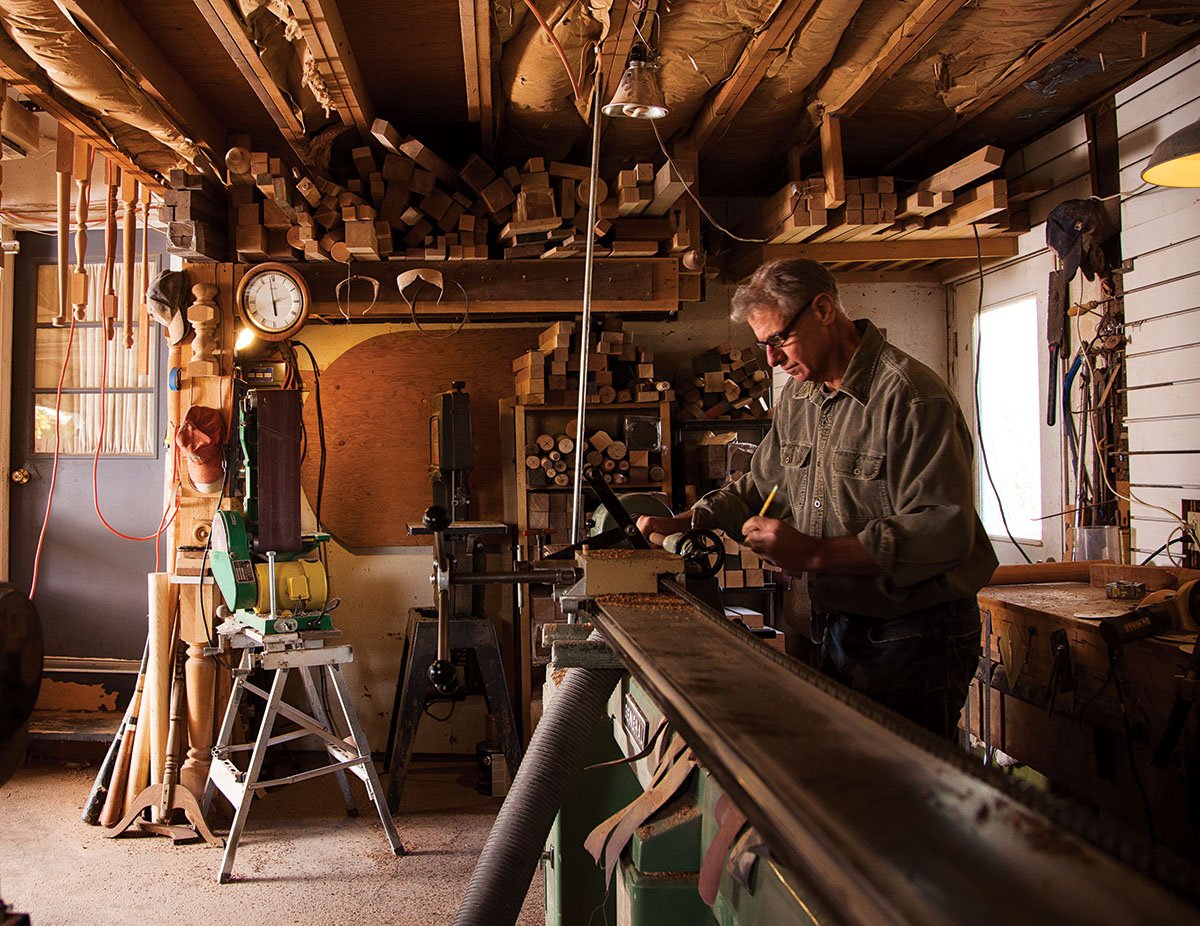
Photo credit: Pat Piasecki
Mast Journal: How did you first learn to turn wood?
Ken Freeman: It really was by chance. I had another career. I was in labor and employee relations, doing hiring and firing, in higher education for quite a few years. I didn't retire by any stretch. I left in my forties because I got tired of it, basically. And we just fell into this. My wife was, believe it or not, at a takeout place and there was a long line. She struck up a conversation with this couple that was looking to sell their woodturning business. And she said, ‘Well, we're trying to figure out our next phase in life.’ And he said, ‘Well, come up.’ We're in the Burlington area and he is 40 miles out of town. I went up and we just hit it off and he felt he could teach me—and he did. We bought the business, moved the equipment down here, and the rest is history. It's been almost 20 years now.
MJ: That’s incredible! And you took to wood turning right away?
KF: Yeah. I grew up around wood, but I had never turned before. Woodturning is a unique niche within the woodworking world and you have to do it regularly or you kind of lose it. It's a skill-oriented thing. If I take four or five days off, I have to warm up a little bit, just to get the muscle memory back. And so a lot of millworkers and woodworkers will do everything except turning. They'll just give their turning work to me.
MJ: It’s very specialized! How did you start making rolling pins?
KF: In 2009, the economy took quite a twist and the construction side of the economy got really bad. So we actually created Vermont Rolling Pins out of desperation in that sense, because business slowed down quite a bit and we had to do something. We started making rolling pins and people from the New York Times and Women's Day somehow discovered them and wrote some articles about us. The business kind of exploded and that's really how things took off.
MJ: That’s awesome. Did you have any background in baking or cooking?
KF: No. Cyndi does. When I grew up, mom's rolling pin was always around and she always used it for her baking. But really, no, I didn't. I just knew that if we were going to make anything that would sell on a retail basis, it needed to be really nice, artisan-type stuff, but also usable, if you're going to hit more of a mass market. And a rolling pin just fits that description perfectly.
MJ: It really does. How did you decide on the designs for your rolling pins?
KF: I can't really design unless it's in the lathe. I just started turning and came up with the acorn design and the beehive design and all these different designs. It's hard to describe if you don't turn, but it just flows with what you're doing at the moment. And that's it really. Of course, we also have traditional designs like the French pin, the Shaker pin, and the big pasta pin. Mast Market always orders our French pins. They're sleek. They come down to a nice point. You’ve got to make them different. Otherwise, why would you spend $15 more than what you’d spend at Bed Bath and Beyond? They're not around anymore, but the equivalent.
MJ: What is the difference between your French rolling pin and one from a big box retailer?
KF: I’m not cutting them down—it’s just different. From a Bed Bath and Beyond equivalent, it’s a straight piece of maple and basic and made in China. It takes a little more time and effort to bring down the ends to about a half inch point. In other words, the taper is much more sleek on my pins. Others start to taper a little bit and then are just chopped off at the end because that’s easier to do with those bigger machines. I individually turn these, so I'm able to bring them down to a really nice, sleek-looking silhouette. That's what people notice the most.
MJ: For sure—it’s an artisan touch. Which of your designs is your favorite?
KF: Personally, I like the Flame, but that's just because it's a little more artisanal. It takes a lot more effort to get it right. They can break while you're turning them. The Shaker, the French, and our long pasta pins, which are 36 to 40 inches, are the three most popular. I hate to short the others—they all sell. But when push comes to shove, many traditional bakers want to stick with handles that they're used to. Or the French, which has no handles. And people love that. You're not restricted to handles in any way.
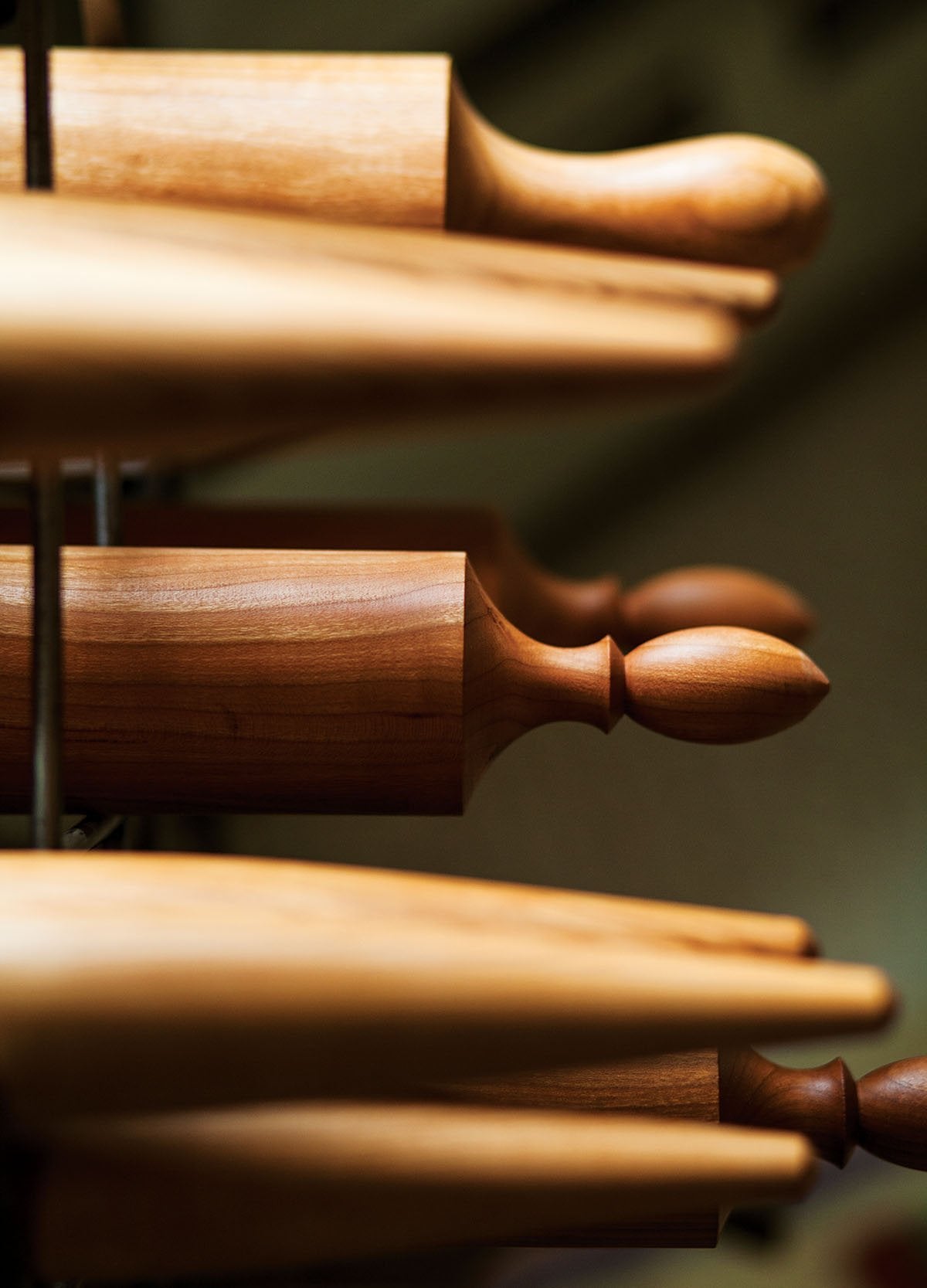
Photo credit: Pat Piasecki
MJ: Totally. What species of wood do you use for your pins? And why did you choose those types?
KF: That's a really good question. It just kind of happened. Maple is traditional, and cherry and walnut are just beautiful woods. So we offer cherry, walnut, and maple. And that’s really it.
MJ: And people can choose which wood they want for any given design?
KF: Right, there’s a drop-down menu on the website. You pick out what you want. We do engraving, as well. And people contact us all the time with maybe a different species that they'd like or their grandmother's broke and they'll send it and I'll replicate it, that sort of thing.
MJ: Oh, that's cool that you do custom work, as well.
KF: Yeah. We say ‘custom woodturning,’ so you can't turn it down. You don't make much money at those, but it's just an added piece of what we offer.
MJ: Makes sense! And how do you finish the rolling pins? Is there a special coating that helps with rolling out dough?
KF: It’s a mineral oil and beeswax combination. It's blended together so it's food safe and it offers up a real good protection to the wood.
MJ: Do they ever need to be refinished?
KF: We recommend just slapping on a real quick coat of mineral oil because it's a household item. I like doing it after every use. If you want it to look like it's brand new, clean it, wipe a quick coat on, and you're good to go.
MJ: That’s great advice. And where do you source the wood from?
KF: I source it, believe it or not, from about three miles from here. But they get it wherever they can get it. I think, typically, some of the maple is from Vermont. The walnut and the cherry are from upstate New York and Pennsylvania, usually.
MJ: That’s still very local!
KF: Yeah, nothing outside of the Northeast, really.
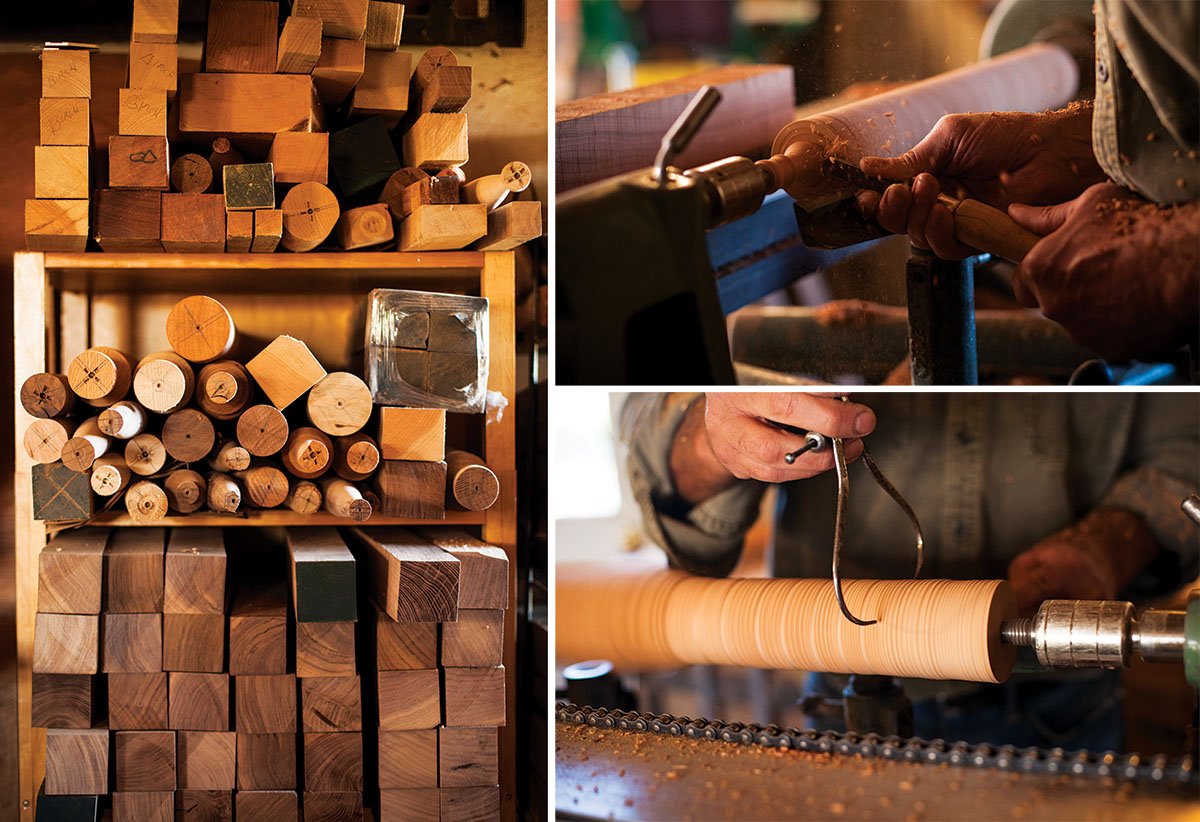
Photo credit: Pat Piasecki
MJ: What is your work schedule like? Are you making rolling pins every day?
KF: It's almost every day. Like most retail sectors, it's going to slow down after Christmas. But normally, I’m making them every day. At this point in time, we're probably making about 20 plus per day, all hand-lathed. The orders are pretty regular, even during the off season, which is anything but the fourth quarter. The fourth quarter is super busy because retailers like Mast are loading up, they're getting their inventory, and then, of course, people are just shopping more in general. Mother's Day is also a busy time. There’s a holiday for everything.
MJ: Oh yeah.
KF: It was hard to get popular, but once we got there, it was steady. My original reaction was, ‘Really? Rolling pins? How many people bake?’ Well, what an idiot I was because there's a huge sector of people who love to bake. And in the Covid year, 2020, it exploded. I said, ‘What's going on here?’ Well, again, I was being an idiot. People were staying home and baking. So there is a market. You just have to hit it nationally and internationally. Otherwise, your slice of the pie, no pun intended, is going to be pretty small.
MJ: Totally. And aside from those first few articles, how did you gain traction?
KF: Initially, we schlepped these pins to trade shows wherever we could go in New England to get our name on the map and get our business cards out there. We tried to direct as many people to the website as possible through just hard work, basically. I always say I'm the worst consumer. I won't read an article about a product and have to have it, but people do. It's amazing. So I go back to those articles because it was so clear that when the New York Times had a big article on us, that really helped us a lot. There was a direct response. There have also been little blurbs in Bon Appétit and other places, so now when you Google, you'll get the Amazons and the Walmarts and then you'll see Vermont Rolling Pins.
MJ: That’s amazing.
KF: I mean, you don't retire early off of rolling pins, but you turn it into a six-figure business and you're able to pay the bills and have a little food.
MJ: Sounds like a nice way to live!
KF: Yeah, the lifestyle is great. I'm sitting here right now in my shop next to the house.
MJ: Oh, your studio is on your property?
KF: Yeah. I converted our two-car garage into a shop. I appreciate you calling it a ‘studio.’ I call it a cave. When you get into this business, you just say, ‘I can't throw this piece of wood away. It's too beautiful.’ So I have stuff everywhere.
MJ: When you’re not making rolling pins or working on architectural and furniture projects, do you still turn wood for fun?
KF: That's a really good question. I actually love it so much that I'll take a time out from a project, whether I can afford to or not, to make cool little things. Right now, I'm making some Christmas trees. I make accent pieces. That's really creative. You just go. You put a piece in the lathe and go. I love it so much that I'll come out before the 4:30 p.m. football game.
MJ: That’s so fun.
KF: I really do enjoy it.
More from The Journal
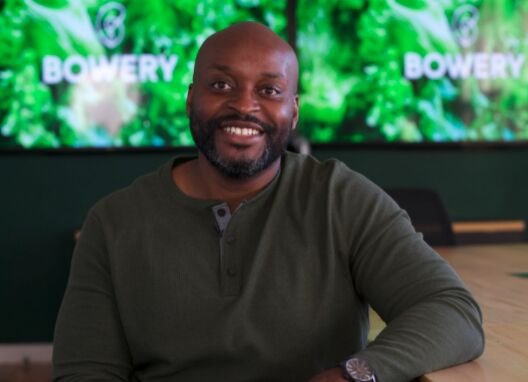
In conversation with Prince Swaray of the vertical farming company, Bowery. He explains what vertical farming is, shares the company’s mission and gives us a taste of the current leafy offerings.
Read more